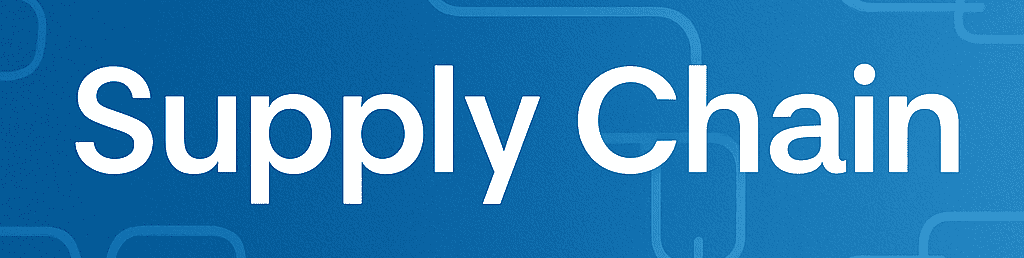
Australia’s National Plastics Plan, released in November 2023, marks a significant regulatory advance in the country’s efforts to reduce plastic waste and promote circular economy practices. At its core, the Plan imposes mandatory upstream reporting requirements on producers, importers, and users of plastic packaging materials. The goal is to create full transparency across the plastics supply chain, enabling regulators, industry, and consumers to track the lifecycle of polymers used in packaging, from resin production through to post-consumer recycling. For Australian consumer goods firms, this introduces new obligations and opportunities to align procurement systems, supplier management processes, and reporting workflows with national sustainability goals.
A key component of the National Plastics Plan is its requirement for packaging producers to submit quarterly disclosures detailing polymer types, volumes, sources, and intended use cases. These reports must be consistent with data standards defined by the Australian Department of Climate Change, Energy, the Environment and Water and must reference material identifiers provided through the Plan’s open data platform. The open data portal, launched alongside the Plan, offers granular datasets on approved polymer grades, registered resin producers, and licensed recyclers. This platform serves as a vital tool for companies seeking to verify supplier declarations, identify approved material sources, and benchmark their plastic consumption against national targets for recycled content and waste reduction.
For Australian consumer goods companies, integrating National Plastics Plan open data into existing enterprise resource planning systems is essential for seamless compliance. Many leading firms rely on SAP procurement modules to manage supplier contracts, purchase orders, and material specifications. By connecting these modules with the open data platform’s API feeds, companies can automate the cross-referencing of resin grades and supplier credentials during procurement. This integration allows firms to flag non-compliant suppliers in real time, prevent the sourcing of unapproved materials, and ensure that packaging components meet regulatory and internal sustainability standards. Further, embedding these checks within procurement workflows helps to streamline the quarterly reporting process, as validated data is captured at the source and aggregated for disclosure.
Developing a robust polymer use disclosure template is a critical step in fulfilling the Plan’s reporting requirements. The template should be designed to align with the structure of the government’s submission portal, ensuring that data can be uploaded without reformatting. Essential elements include the reporting period, total polymer volumes used by type (for example, PET, HDPE, LDPE, PP, PS), the proportion of virgin versus recycled content, supplier names and registration numbers, and material end-use categories (such as primary packaging, secondary packaging, or tertiary logistics materials). Companies should also document any third-party certifications or audits that verify recycled content claims or material traceability. Where possible, the template should include embedded data validation rules to prevent common errors, such as misreporting of polymer codes or omission of mandatory fields.
Establishing the internal processes to support accurate quarterly reporting requires cross-functional collaboration between sustainability, procurement, supply chain, and IT teams. Procurement teams must work closely with suppliers to collect and verify material data at the point of purchase. Sustainability teams are responsible for aligning reporting outputs with corporate ESG objectives and regulatory requirements. IT teams play a pivotal role in configuring ERP and procurement platforms to support data integration, validation, and reporting automation. By fostering these cross-functional partnerships, companies can reduce the risk of non-compliance, improve the quality of their disclosures, and generate insights that drive continuous improvement in packaging sustainability.
Beyond compliance, the transparency mandated by the National Plastics Plan offers consumer goods firms an opportunity to strengthen their brand positioning. Consumers and business partners increasingly expect credible evidence of environmental responsibility. By publishing summaries of quarterly polymer use reports in annual sustainability reports or on corporate websites, firms can demonstrate accountability and leadership in addressing plastic waste challenges. These summaries can highlight achievements such as increases in recycled content, reductions in total polymer use, or successful supplier engagement initiatives. Over time, such disclosures contribute to building stakeholder trust and enhancing the company’s social license to operate.
The National Plastics Plan represents a major shift in how plastic use is managed and reported in Australia. While compliance introduces new complexities, it also creates a framework for companies to embed sustainability more deeply into their supply chain operations. By integrating National Plastics Plan open data with SAP procurement modules, Australian consumer goods firms can automate compliance processes, improve data accuracy, and unlock valuable insights for continuous improvement. A well-designed polymer use disclosure template, coupled with strong internal governance and supplier engagement, will ensure that companies not only meet regulatory requirements but also lead the transition to a more circular, responsible plastics economy.